Posted At: Jul 11, 2025 - 114 Views
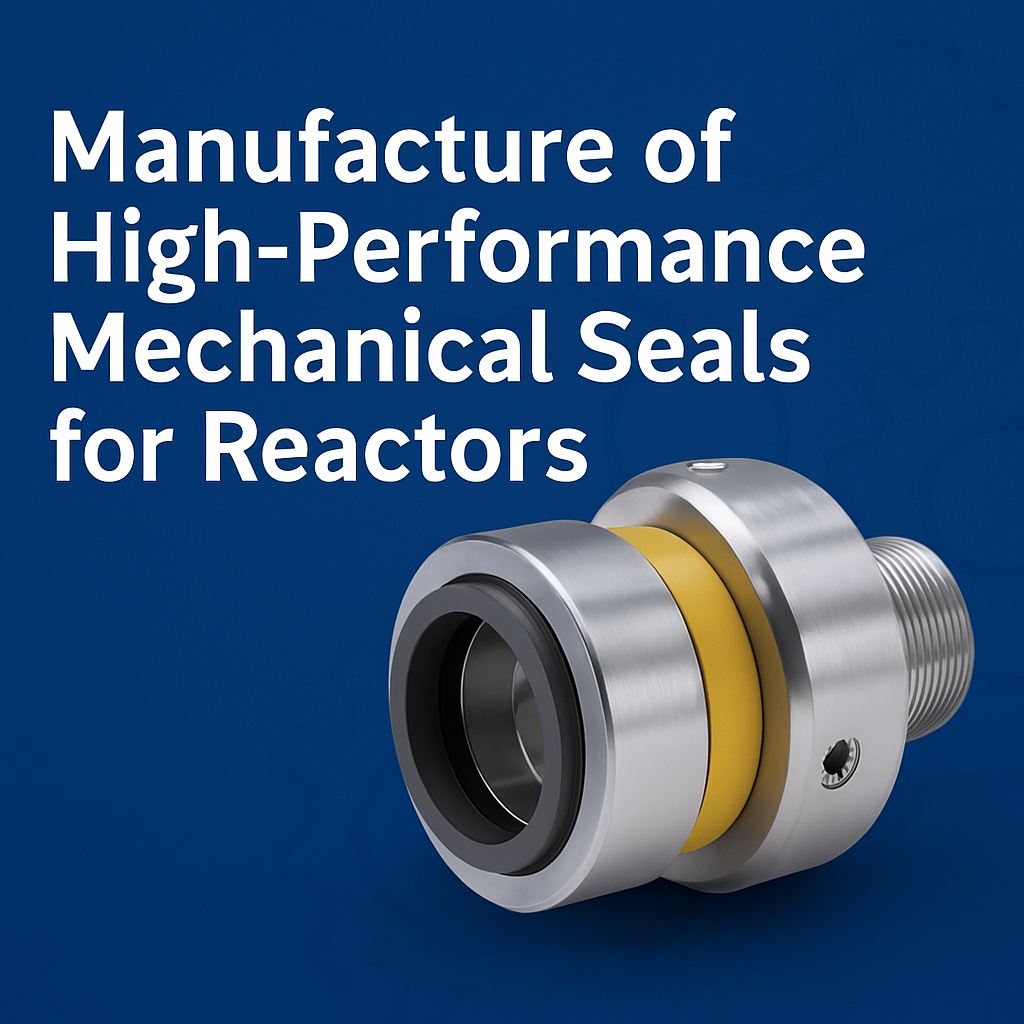
Manufacture of High-Performance Mechanical Seals for Reactors
In industries like pharmaceuticals, chemicals, and food processing, reactors are critical components that demand absolute sealing reliability. To prevent leaks, maintain pressure, and ensure safe operations, high-performance mechanical seals are essential. At QMSeals, we specialize in designing and manufacturing advanced sealing solutions tailored for reactor applications across various industries.
This article dives into the process of manufacturing mechanical seals for reactors, explores the different reactor mechanical seal types, and explains how to choose the right seal based on your industry’s operational demands.
What Are Reactor Mechanical Seals?
Reactor mechanical seals are used to seal the rotating shaft in agitated reaction vessels (like glass-lined or stainless steel reactors). These seals are specifically engineered to operate under extreme process conditions such as:
High temperature and pressure
Aggressive and corrosive media
Vacuum or pressure cycles
Cleaning-In-Place (CIP) and Sterilization-In-Place (SIP) protocols, commonly required in pharmaceutical and food processing industries.
With over a decade of experience in mechanical seal design, QMSeals delivers tailor-made sealing solutions for demanding reactor systems.
Why High-Performance Reactor Seals Matter
Seal failures in reactors can result in serious consequences — including hazardous leaks, environmental hazards, product contamination, and expensive operational downtime. Choosing high-performance mechanical seals helps ensure:
Leak-proof operations
Reduced maintenance frequency
Longer operational life
Compliance with industry standards (ATEX, FDA, GMP)
Enhanced workplace and environmental safety
QMSeals’ Manufacturing Process for Reactor Mechanical Seals
At QMSeals, each reactor seal is manufactured with precision, care, and custom engineering to match your exact application needs.
1. Client Requirement & Application Assessment
We begin by gathering all necessary process data:
Media type (acidic, abrasive, toxic, sterile)
Operating pressure and temperature
Shaft size and RPM
Reactor vessel type (glass-lined, SS, jacketed)
Compliance requirements (API, GMP, etc.)
2. Seal Design & Configuration
Using CAD and simulation software, we engineer custom seal designs. Key focus areas include:
Dynamic sealing elements (balanced or unbalanced)
Material selection based on chemical compatibility
Flush plan design (API 682 options)
Thermal management to handle high heat zones
3. Material Selection
QMSeals uses premium-grade materials to ensure resistance to corrosion, wear, and chemical attack:
Seal Faces: Silicon Carbide, Tungsten Carbide, Resin-Impregnated Carbon
Elastomers: FEP, Kalrez®, PTFE, Viton®
Metal Parts: SS316L, Hastelloy C, Alloy 20, Inconel
4. Precision Machining & Polishing
Critical sealing surfaces are machined to micron-level tolerances using advanced CNC machinery. Seal faces are polished to optical flatness for low friction and effective sealing.
5. Clean Room Assembly
To avoid contamination, seals are assembled in a controlled clean room. Pre-assembled cartridge seals are available for easy installation and reduced human error.
6. Testing & QA
Every seal undergoes rigorous testing:
Hydraulic and pneumatic pressure testing
Vacuum leak testing
Torque and alignment inspection
Material traceability and performance validation
Types of Reactor Mechanical Seals Offered by QMSeals
Choosing the right seal depends on your reactor's configuration, media, and operating environment. At QMSeals, we offer all major reactor mechanical seal types:
1. Single Mechanical Seal
Ideal for non-hazardous applications
Compact and cost-effective
Requires external flush in many cases
2. Double Mechanical Seal (Back-to-Back or Face-to-Face)
Preferred for toxic, volatile, or hazardous media
Uses a barrier fluid between the seals
Offers added safety and zero-emission operation
3. Tandem Mechanical Seal
Used in critical applications with pressure variations
One seal acts as backup in case the primary fails
Effective for pharma, biotech, and food industries
4. Dry Running Seals
No need for external lubrication
Used in batch reactors or sterile processes
Reduces contamination risk
5. Gas-Lubricated Mechanical Seals
Utilizes nitrogen or clean gas
Excellent for ultra-pure or dry-running environments
Popular in cleanroom and aseptic reactors
6. Cartridge Reactor Seals
Pre-assembled and pre-set seals
Easy installation and minimal maintenance
Widely used for high uptime requirements
Industries We Serve
QMSeals provides reactor seal solutions for:
Pharmaceuticals: Aseptic, GMP, and CIP-compatible seals
Chemicals: Highly corrosion-resistant seals for acids, solvents
Food & Beverage: Hygienic seals with FDA-compliant materials
Paints and Pigments: Seals that handle abrasive slurries
Biotechnology: Clean and contamination-free operations
Key Benefits of QMSeals Reactor Seals
Custom-built for your reactor dimensions
Reliable sealing even under vacuum or high pressure
Long service life and low maintenance
Available in both standard and exotic materials
Full technical support from selection to installation
How to Select the Right Reactor Mechanical Seal
Here's what to consider before selecting a seal:
Factor | Description |
---|---|
Media | Is it corrosive, abrasive, toxic, or sterile? |
Pressure/Temperature | Helps determine materials and face design |
Shaft RPM and Runout | Affects balancing and dynamic performance |
Compliance Needs | GMP, FDA, ATEX, API, etc. |
Installation Constraints | Vertical/horizontal shafts, space limitations |
Not sure what suits your reactor best? Our technical team can help you select the right solution.
Why Choose QMSeals for Reactor Seal Manufacturing?
At QMSeals, we understand the complexities involved in sealing rotating equipment inside reactors. With our vast experience, high-precision engineering, and deep industry knowledge, we are your reliable partner for reactor mechanical seals.
We offer:
Custom sealing solutions
Fast lead times
Full lifecycle support
Industry-compliant designs
Competitive pricing
Conclusion
The manufacture of high-performance mechanical seals for reactors is a specialized process that requires precision, advanced materials, and deep application knowledge. Selecting the right seal not only boosts process efficiency but also ensures environmental safety, operator protection, and equipment longevity.
Understanding various reactor mechanical seal types helps engineers and procurement teams make better decisions. Whether it's a pharmaceutical reactor needing GMP-compliant seals or a chemical plant requiring corrosion-resistant solutions, the right seal can significantly influence performance.
Frequently Asked Questions
1. What are the common types of mechanical seals used in reactors?
Single seals, double seals, tandem seals, cartridge seals, and gas-lubricated seals are commonly used based on application.
2. Can mechanical seals be customized for my reactor design?
Yes, QMSeals offers fully custom-designed reactor seals to fit your shaft, vessel, and media requirements.
3. How often do reactor mechanical seals need replacement?
With proper lubrication and alignment, QMSeals’ reactor seals can operate reliably for several years depending on usage.
4. Do you offer seals for glass-lined reactors?
Absolutely. We offer seal solutions compatible with glass-lined reactors and corrosive chemical applications.
5. What makes QMSeals different from other manufacturers?
We combine precision manufacturing with personalized technical support and fast service to ensure optimal performance in your reactors.