Posted At: May 16, 2025 - 306 Views
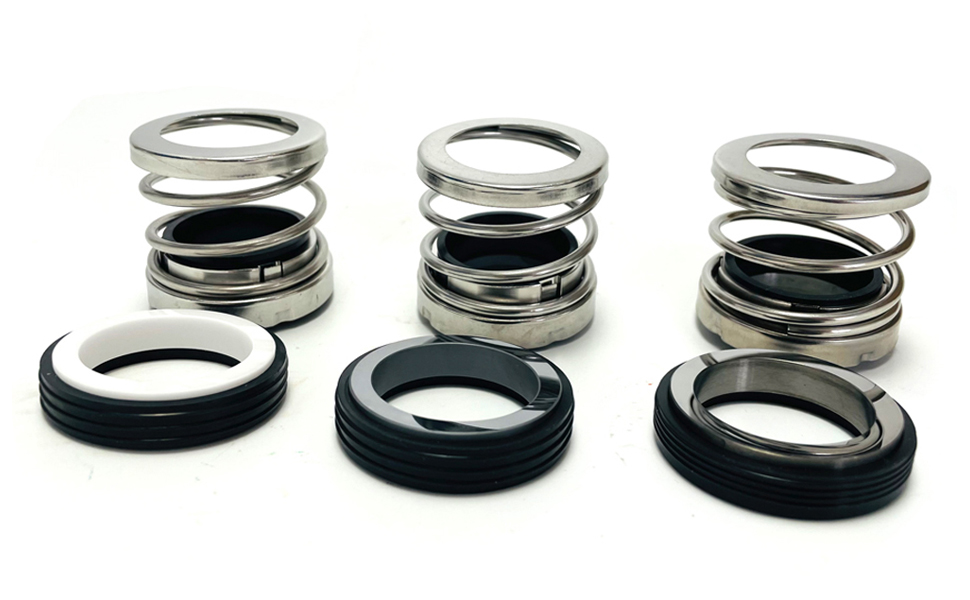
How Mechanical Seals Are Used for Leakage Prevention
When it comes to rotating equipment such as pumps, mixers, or compressors, mechanical seals play a critical role in preventing leakage. These components may seem small, but their function is vital to ensuring the efficiency, safety, and reliability of countless industrial systems. In this blog, we’ll explore how mechanical seals work, why they are essential for leakage prevention, and how they’re used across various industries.
What Are Mechanical Seals?
Mechanical seals are devices used to join systems or mechanisms together and prevent leakage, especially in situations where parts are moving relative to each other. They are commonly used in equipment with rotating shafts — such as pumps — where they help contain fluid within the system while keeping contaminants out.
The seal works by creating a barrier between the rotating shaft and the stationary pump housing. This barrier is crucial for maintaining the internal pressure, avoiding fluid loss, and preventing environmental contamination.
Why Leakage Prevention Matters
Leakage in rotating equipment can lead to:
Environmental hazards (especially in chemical or petroleum industries)
Increased maintenance costs
Equipment failure
Safety concerns for workers
Loss of valuable product
In high-performance industrial applications, even a small leak can result in downtime or legal violations. That’s why reliable sealing systems like mechanical seals are essential.
How Do Mechanical Seals Work?
A mechanical seal typically consists of the following components:
Rotating seal face (primary ring) – Connected to the shaft and spins with it.
Stationary seal face (mating ring) – Fixed to the pump housing.
Secondary seals – Usually O-rings or gaskets that prevent fluid from leaking around the seal faces.
The spring or bellows mechanism maintains optimal pressure to ensure the seal faces remain in proper contact.
Principle of Operation
The core of a mechanical seal lies in the interface between its two seal faces-one that rotates and one that remains stationary. These faces are manufactured to extremely tight tolerances and polished to reduce friction.
When the equipment operates, a thin fluid film forms between the faces. This film acts as a lubricant, reducing wear and maintaining a seal. If the seal faces separate too much, leakage can occur. If they press too hard, they may wear out quickly.
The balance is delicate — and that’s why mechanical seals are designed with precision engineering.
Types of Mechanical Seals
There are various types of mechanical seals, each designed to meet the needs of specific applications:
1. Pusher Seals
Springs are used to maintain contact between the seal face and the mating ring by exerting constant pressure. Common and cost-effective, but less ideal for high-pressure or high-temperature conditions.
2. Non-Pusher Seals
These feature a metal bellows in place of springs, offering improved performance in extreme conditions and greater resistance to clogging and contamination.
3. Cartridge Seals
Pre-assembled and factory-tested, making installation much easier and safer. Ideal for reducing installation errors.
4. Balanced Seals
Reduce the load on the seal faces, which decreases wear and extends lifespan. Perfect for high-pressure applications.
5. Unbalanced Seals
Less expensive but more prone to wear under high pressure. Suitable for low-pressure systems.
Mechanical Seals vs. Traditional Packing
Before mechanical seals became common, stuffing box packing (such as braided rope and grease) was used to control leakage. While simple and cheap, packing wears quickly and requires frequent adjustments and replacements.
Advantages of Mechanical Seals:
- Lower maintenance
- Longer lifespan
- Less friction and power consumption
- Better leakage control
- Environmentally safer
Over time, mechanical seals have proven to be the superior solution in most modern industrial settings.
Applications of Mechanical Seals
Mechanical seals are used in a wide variety of industries and equipment types, including:
- Chemical processing
- Petroleum refineries
- Water treatment plants
- Food and beverage manufacturing
- Pharmaceutical production
- HVAC systems
In each of these settings, the goal remains the same: to prevent fluid leakage while allowing rotation or movement.
Factors That Affect Seal Performance
1. Operating Conditions - Temperature, pressure, and fluid properties (like abrasiveness or corrosiveness) all impact seal performance.
2. Material Selection - Seal faces are made from materials like carbon, ceramic, tungsten carbide, or silicon carbide depending on the application.
3. Installation Quality - Even the best mechanical seal can fail if installed improperly. That’s why many users prefer cartridge seals — they minimize human error.
4. Maintenance and Monitoring - Routine inspection and lubrication (if required) can extend the life of a mechanical seal. Modern systems also use sensors to monitor seal health.
Innovations in Mechanical Seal Technology
Recent advancements have made mechanical seals more reliable and easier to use:
Dry-running seals for applications without lubrication
Split seals that simplify installation on large equipment
Double seals for high-risk applications with backup protection
Seal support systems (like flush plans) to improve cooling and lubrication
Conclusion
Mechanical seals are indispensable components for modern machinery, especially in applications where leakage prevention is non-negotiable. Their design and material choices are constantly evolving to meet the demanding needs of industries ranging from energy to pharmaceuticals.
By choosing the right seal, installing it properly, and maintaining it well, companies can drastically reduce equipment downtime, improve safety, and protect both people and the environment.
Frequently Asked Questions
1. What is the main function of a mechanical seal?
The primary function of a mechanical seal is to prevent fluid leakage between a rotating shaft and a stationary pump housing. It keeps the process fluid inside the equipment while protecting it from external contaminants.
2. How long does a mechanical seal typically last?
The lifespan of a mechanical seal depends on several factors like operating conditions, fluid type, and maintenance practices. On average, a well-installed mechanical seal can last 1 to 5 years, or even longer in optimal conditions.
3. Can mechanical seals be used with all types of fluids?
Yes, but the materials used in the seal must be compatible with the fluid. For example, corrosive chemicals may require seal faces made from silicon carbide or tungsten carbide, while water or oil may work fine with carbon or ceramic faces.
4. What causes mechanical seals to fail?
Common causes of mechanical seal failure include:
- Improper installation
- Dry running (lack of lubrication)
- Incorrect material selection
- Excessive vibration or misalignment
- Contaminants in the fluid
5. What is the difference between a single and double mechanical seal?
A single seal has one set of seal faces and is used in less critical applications. A double seal has two sets of seal faces (in tandem or back-to-back) and provides an extra layer of protection, especially for hazardous or high-pressure fluids.