Posted At: Jul 07, 2025 - 89 Views
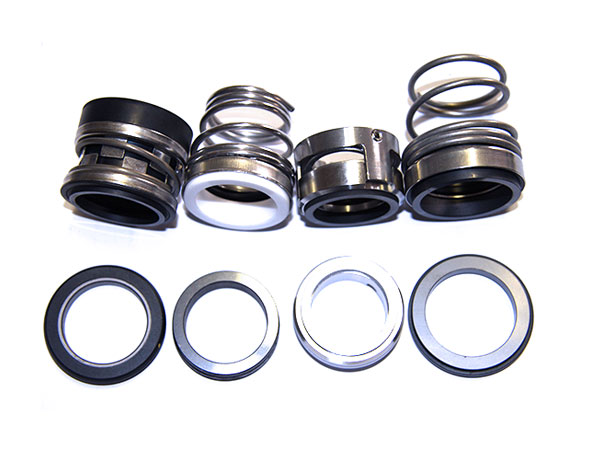
Mechanical Seals: What They Are & Why They Matter
A mechanical seal is a specialized device used in rotating equipment—think pumps, mixers, or compressors—to prevent fluid or gas from leaking along a shaft that passes through a stationary housing. Unlike older. packing-based seals, mechanical seals provide efficient sealing, reduced maintenance, less wear, and enhanced reliability.
Core Components of a Mechanical Seal
1. Rotating Face
Mounted on the shaft and spins with it.
Made of materials like carbon, ceramic, or silicon carbide.
Works as one side of the primary seal interface.
2. Stationary Face (Mating Ring)
Fixed within the seal housing and remains stationary.
Paired with the rotating face to create a tight seal.
3. Secondary Seals
O‑rings, gaskets, bellows, or wedges seal all other connections in the seal assembly.
Prevent any fluid bypass around the primary sealing faces.
4. Load Mechanism (Spring or Bellows)
Applies force to keep the faces in contact.
Compensates for wear and accommodates shaft misalignment.
5. Drive Elements
Drive pins, set screws, or clamp collars connect the rotating face to the shaft.
Prevent slipping and maintain synchronized rotation.
6. Peripheral Hardware
Includes gland plate, sleeve, and housing components to hold the seal tightly in position.
How Mechanical Seals Work
Contact Between Sealing Faces - A rotating face spins against a stationary face under controlled pressure, forming the primary seal
Hydraulic & Spring Loading - A combination of process pressure and spring/bellows tension ensures consistent face engagement.
Lubrication - A microscopic film of the fluid being sealed—often just a vapor—fills the gap between faces. This lubrication prevents overheating and wear while minimizing leakage.
Leakage Control - The ultra-thin lubricant film allows almost no visible leakage—typically around half a teaspoon per day—while still ensuring functionality.
Secondary Seals Prevent Bypass - O‑rings or bellows seal all other potential pathways—only the faces are allowed to leak at that minimal, controlled rate.
Types of Mechanical Seals
Single vs. Double:
Single seals serve most standard applications. Double seals—either tandem or face-to-face—add a barrier fluid between the two seal sets, ideal for hazardous fluids.
Pusher vs. Non‑Pusher:
Pusher seals use dynamic O‑rings and springs to adjust the seal over time.
Non‑pusher (bellows) seals rely on metal or elastomer bellows and avoid sliding secondary seals.
Cartridge vs. Component Seals:
Cartridge seals arrive pre‑assembled—simplifying installation and reducing error. Component seals are built piece by piece, offering flexibility but requiring careful assembly.
Why Materials Matter
Seal Faces
Carbon is common for general use; silicon carbide and tungsten carbide resist wear and abrasion. Ceramic provides chemical resistance.
Secondary Seals
The selection of elastomers—like Viton®, EPDM, Aflas®, and Kalrez®—is guided by their resistance to chemicals and operating temperatures.
Advantages of Mechanical Seals
Virtually no visible leakage
Reduced energy loss compared to packing
Minimal shaft damage and less maintenance
Ideal for hazardous or abrasive environments.
Applications Across Industries
Widely used in garbage trucks, water treatment plants, petrochemical systems, pharmaceutical lines, power generation, and food & beverage processing—essentially any system involving rotating shafts and fluids .
Tips for Proper Use & Longevity
- To ensure reliable operation and longer seal life:
- Use proper assembly and installation guidelines
- Keep shaft and housing clean, aligned, and free of damage
- Prevent dry-running by maintaining lubrication
- Monitor seal for vibration, heat, and leaks
- Inspect components regularly and replace worn parts.
Conclusion
A mechanical seal is a finely balanced system of precisely machined faces, robust loading mechanisms, and carefully selected materials. Its transparent leakage mechanism trades negligible vapor loss for reliable, maintenance-free operation, making it a game-changer compared to traditional packing solutions.
Frequently Asked Questions
1. What is the purpose of the spring in a mechanical seal?
The spring keeps the seal faces in contact to prevent leakage and maintain sealing pressure as components wear.
2. Can mechanical seals be reused?
It is generally not recommended. Once a mechanical seal is removed, its integrity may be compromised.
3. How do I choose the right mechanical seal material?
Consider the fluid type, temperature, pressure, and shaft speed. For corrosive environments, use high-performance materials like PTFE or Hastelloy.
4. What’s the difference between a component seal and a cartridge seal?
A component seal consists of separate parts and requires assembly during the installation process. A cartridge seal is pre-assembled, simplifying installation and reducing error.