Posted At: May 15, 2025 - 314 Views
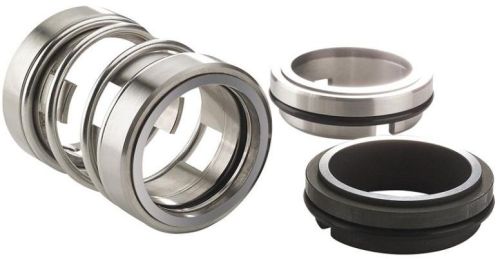
The Role of Single Mechanical Seals
When it comes to ensuring the smooth operation of pumps, compressors, and other rotating equipment, the single mechanical seal is often the unsung hero. These small yet powerful components are essential for sealing systems, preventing leakage, and maintaining system efficiency in a variety of industries—from chemical processing to water treatment.
In this blog, we’ll explore what single mechanical seals are, why they’re necessary, and how choosing the right seal can save your business time, money, and maintenance headaches.
Why Are Single Mechanical Seals Important?
1. Leak Prevention
The primary role of any mechanical seal is to stop fluids (liquids or gases) from leaking out of a machine. Single mechanical seals are particularly effective in applications where low-pressure systems or clean liquids are involved.
2. Protect Equipment
Fluid leakage can lead to corrosion, overheating, or contamination of other components. A properly installed single mechanical seal protects bearings, shafts, and other moving parts from damage—extending equipment life.
3. Reduce Operating Costs
Mechanical seals reduce the need for frequent maintenance. Unlike gland packing, which requires regular tightening and replacement, single seals operate with minimal intervention.
Applications of Single Mechanical Seals
Single seals are used in many industries, including:
Water & Wastewater Treatment - Used in centrifugal pumps to seal clean or slightly contaminated water.
HVAC Systems - Single seals are ideal for circulating pumps in heating and cooling systems.
Food & Beverage Processing - Their simple design and hygienic materials make them suitable for sanitary applications.
Pharmaceuticals - Where a reliable and sterile seal is needed for fluid transfer.
Benefits of Using a Single Mechanical Seal
Cost-Effective
Because they’re simple and use fewer components, single mechanical seals are more affordable to manufacture and install than double seals.
Compact Design
Ideal for machines with limited installation space. Their low profile allows for easy retrofitting into older equipment.
Easy Installation
They can often be installed without the need for extensive disassembly, reducing downtime.
Energy Efficient
Because they reduce friction and heat generation compared to packing, they help save energy during machine operation.
Choosing the Right Single Mechanical Seal
Not all seals are created equal. Here’s what to consider:
Material Compatibility - Make sure the seal material matches the fluid it will contact (e.g., Viton for chemicals, EPDM for water).
Temperature and Pressure Range - Check the operating range to avoid premature wear.
Rotational Speed - High-speed shafts require seals with superior thermal and wear resistance.
Application Environment - Clean water systems might need a basic seal, while slurry pumps need more rugged designs.
How to Maintain a Single Mechanical Seal
Maintenance is minimal, but essential. Here’s how to get the most out of your seal:
Regular Visual Inspections – Check for any leaks or surface wear.
Ensure Proper Lubrication – Use the right flush plan to keep the seal faces clean.
Avoid Dry Running – Operating a pump without liquid causes seal faces to overheat and fail.
Replace Worn Seals Promptly – Don’t wait for a catastrophic failure.
Conclusion
The single mechanical seal may be small, but its role in industrial applications is massive. It ensures leak-free operation, reduces maintenance, and keeps systems running efficiently. For applications dealing with clean, low-pressure fluids, there’s often no better choice.
Whether you're working in water treatment, food processing, or HVAC systems, investing in the right seal can drastically improve performance and cut down operational costs.
Frequently Asked Questions
Can I use a single mechanical seal for slurry?
Not recommended. For abrasive or slurry services, a double seal or specialized slurry seal is more suitable.
How long do single mechanical seals last?
With proper installation and maintenance, they can last 2-5 years depending on the application.
What causes a single mechanical seal to fail?
Common reasons include dry running, misalignment, improper installation, or material incompatibility.
What is a single mechanical seal?
A single mechanical seal is a device used to prevent fluid leakage in rotating equipment like pumps by sealing the gap between the rotating shaft and stationary housing.
Where are single mechanical seals commonly used?
They are widely used in clean fluid applications such as water treatment, HVAC systems, food processing, and pharmaceuticals.