Posted At: May 13, 2025 - 116 Views
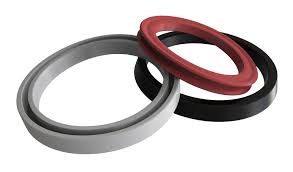
Where O Rings Are Used?
Introduction
O-rings may seem like minor components, but they play a major role in sealing technology across countless industries. These torus-shaped rings are designed to prevent the leakage of gases or liquids in mechanical systems. Their simplicity, cost-effectiveness, and adaptability make them the go-to sealing solution in everything from industrial pumps to aerospace applications.
In this blog, we’ll explore where O-rings are used, different O ring types, and why they're crucial for the performance and reliability of mechanical systems.
What Is an O Ring?
An O-ring is a circular elastomeric seal that fits into a groove and compresses during assembly between two or more parts to form a leak-proof seal. They are commonly made from materials like:
Nitrile (NBR)
Viton (FKM)
EPDM
Silicone
PTFE
These materials offer a range of resistance to heat, chemicals, pressure, and environmental exposure, making O-rings suitable for a variety of applications.
Key O Ring Uses Across Industries
1. Pumps and Valves
O-rings are a critical sealing element in centrifugal pumps, gear pumps, and piston pumps, where they prevent internal leakage of liquids and gases. They’re also widely used in industrial valves to seal pressure zones and enhance system safety.
For a complete guide on choosing the right seal for pumps, check out our blog: How to Choose the Best Mechanical Seal for Your Pump.
2. Hydraulic and Pneumatic Systems
In hydraulic cylinders and pneumatic actuators, O-rings seal pressurized air or oil. These systems rely heavily on O-rings for both static and dynamic sealing, especially in moving components like pistons and rods.
Durable, abrasion-resistant O-rings are essential in preventing system leaks and maintaining energy efficiency.
3. Automotive Applications
Automotive engines, gearboxes, fuel systems, and brake assemblies use O-rings to contain fluids and maintain pressure. Whether it's sealing engine oil, transmission fluid, or fuel lines, O-rings help prevent breakdowns and increase efficiency.
Due to exposure to heat and oil, materials like Viton and NBR are commonly used in automotive O-rings.
4. Food and Beverage Industry
Food-grade O-rings are vital in processing machinery, such as mixers, bottling lines, and dairy systems. They must comply with FDA or EU regulations and withstand regular exposure to steam, hot water, and cleaning agents.
EPDM and Silicone are often preferred materials for their chemical resistance and hygiene compatibility.
5. Pharmaceutical and Medical Equipment
In this industry, precision, safety, and hygiene are paramount. O-rings are used in devices such as IV pumps, autoclaves, and lab instruments. Medical-grade silicone O-rings provide excellent temperature stability and low toxicity.
They must also endure repeated sterilization cycles and comply with stringent biocompatibility standards.
6. Oil & Gas Industry
O-rings in oil rigs, drilling tools, and subsea systems must handle extreme pressure, high temperatures, and aggressive chemicals. Materials like FKM, FFKM, and HNBR are ideal for these environments.
Applications include:
- Downhole drilling equipment
- Pipeline connectors
- Wellhead seals
- Blowout preventers
7. Aerospace and Aviation
Aircraft hydraulic systems, fuel valves, and engine components rely on high-performance O-rings. These applications demand extreme resistance to pressure, vacuum, temperature, and chemical exposure.
Aerospace-grade O-rings often undergo rigorous testing for durability and safety in high-altitude conditions.
8. Electrical and Electronic Enclosures
To protect sensitive electronics from dust, water, and moisture, O-rings are used in enclosures, switches, connectors, and control panels — especially in outdoor or marine environments.
IP-rated enclosures often feature O-rings as a primary sealing mechanism.
Common O Ring Types Based on Material
Choosing the correct O-ring depends on the application and the operating environment. Here are some common O ring types based on material:
Material | Features | Applications |
---|---|---|
Nitrile (NBR) | Oil-resistant, flexible, cost-effective | Automotive, hydraulics |
Viton (FKM) | Heat and chemical resistant | Aerospace, oil & gas |
EPDM | Steam, ozone, and water resistant | Food-grade, water filtration |
Silicone | High temp resistance, biocompatible | Medical devices, electronics |
PTFE (Teflon) | Excellent chemical resistance, low friction | Aggressive chemicals, pharma equipment |
FFKM | Extreme heat & chemical resistance | Semiconductor, oil & gas |
Why O Rings Are Essential in Mechanical Systems
Leak Prevention: O-rings provide a tight seal to prevent loss of fluids or gases.
Compact Design: Requires minimal space, making it ideal for tight assemblies.
Reliability: Long-lasting and durable under pressure and friction.
Versatility: Suits both static and dynamic applications across industries.
Cost-Effective: Inexpensive yet critical for high-performance sealing.
How to Select the Right O Ring
When selecting an O-ring, consider:
- Operating temperature and pressure
- Chemical compatibility
- Dynamic vs. static application
- Material certifications (e.g., FDA, aerospace, etc.)
- Proper sizing and groove design
Consulting with a seal supplier can ensure you choose the optimal type for your specific application.
Conclusion:
O-rings are essential components in nearly every industry that relies on machinery. From heavy industrial pumps to precise medical instruments, the performance of O-rings can determine the reliability and efficiency of the system.
Understanding the various O ring uses and O ring types can help businesses make informed decisions and prevent costly failures. When you’re working with pumps or fluid systems, make sure to select the right sealing solution — because a small ring can make a huge difference.